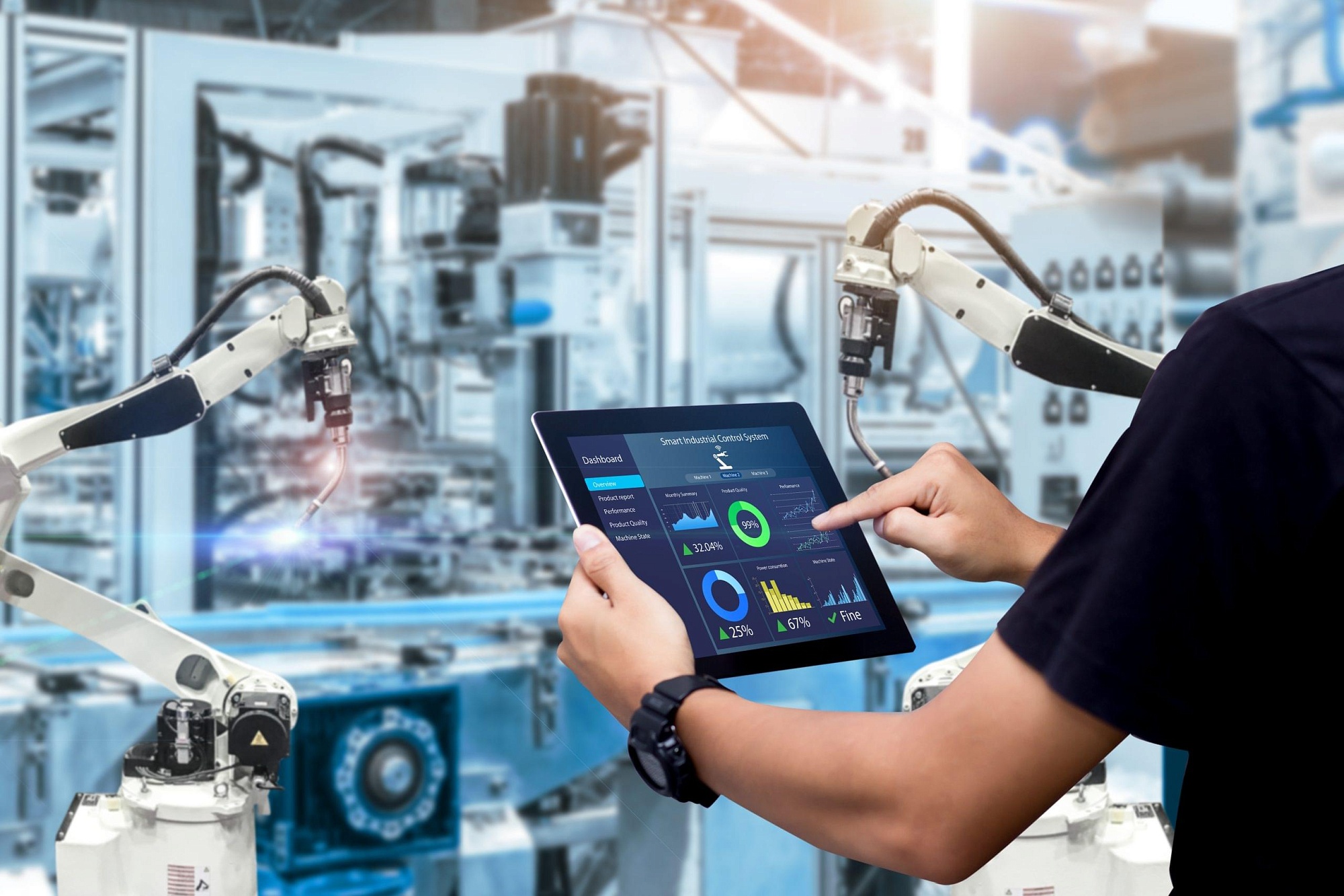
Современное предприятие уже невозможно представить без ИТ-систем: на каждом этапе цепочки создания стоимости не обойтись без специализированных решений. Эксперты практики «Производство» консалтинговой компании Odyssey Consulting Group Алексей Чеславский и Дмитрий Боголюбов делятся рациональным подходом к автоматизации производств.
Планирование автоматизации необходимо как для компаний, развивающих свою ИТ-систему, так и для компаний, строящих ее с нуля. Существуют два основных подхода к планированию системы автоматизации:
1. Создать единое программное решение, которое будет включать в себя всю функциональность, необходимую компании,
2. Собрать комплекс ИТ-решений, отвечающих за функциональные блоки, и интегрировать их между собой.
Несмотря на кажущуюся логичность первого подхода, мы не рекомендуем выбирать именно его по нескольким причинам.
Во-первых, специализированное ПО разработано с учетом нюансов и деталей, важных для конкретного функционального блока. Для сложного специализированного оборудования, например, компании-производители или эксплуатанты (собственное ПО) самостоятельно разрабатывают ИТ-решения для управления оборудованием и персоналом на уровне цеха, линии, групп оборудования в зависимости от свойств производственного процесса. Это означает, что все необходимые функции в таких решениях реализованы с точки зрения максимального удовлетворения требований производства.
Во-вторых, для любой системы, даже самой современной, нельзя гарантировать отсутствие сбоев и неполадок. Единое программное решение для всей компании не позволяет нивелировать данный риск путем обособления отдельных интегрированных в единую систему ИТ решений и функций: если система станет не доступна, ни один из пользователей ни в одном подразделении компании не сможет получить доступ к системе. Это ведет к простою всей компании, в том числе критических для бизнеса функций. Вероятность каскадного сбоя в едином программном решении в разы выше. Например, сбой в подсистеме управления данными НСИ может привести к каскадному возникновению ошибок по всей системе (производство, склад, закупки, продажи и т.д.).
В-третьих, чем больше модификаций в системе, тем выше риск ошибок, которые могут вывести из строя всю систему предприятия целиком. Это дополнительно увеличивает необходимость в серьезной технической поддержке системы. Напротив, ИТ-решения в интегрированной системе обособлены друг от друга на уровне функций, определена их критичность для бизнеса, поэтому наибольшие усилия команд поддержки и сопровождения заказчики могут сосредоточить именно в критических точках системы.
Таким образом, наиболее эффективным и рациональным способом является создание комплекса специализированного набора ПО для автоматизации отдельных функций предприятия и его интеграция в единую систему, что и будет являться системой автоматизации. Такой подход стал распространяться около 5 лет назад в практике автоматизации промышленных предприятий как отвечающий требованиям современных компаний к достижению финансовых и производственных целей.
Приведем пример из практики. Наш клиент, производственная компания полного цикла, привлекла Odyssey Consulting Group для комплексной автоматизации предприятия. Для максимизации функциональности и безопасности системы мы предложили комплекс ИТ-решений: отдельно стоящие системы ERP, CRM, финансового учета и отчетности и APS-систему для оптимизационного планирования производства, чтобы клиент мог осуществлять не только верхнеуровневое планирование производственных процессов, но и оптимизацию ежедневных планов производства с учетом текущей ситуации в производстве для достижения целей, стоящих перед подразделением. Все эти специализированные ИТ-решения были интегрированы между собой в единую систему автоматизации производственного предприятия.
Во внедрении, аналогично, существуют два подхода:
1. Детальное планирование всех аспектов функциональности будущей системы от верхнеуровневых задач до дизайна интерфейса каждого окна,
2. Agile-подход: внедрение системы короткими итерациями и оперативная проверка функциональности с дальнейшей корректировкой следующих блоков системы.
Аналогично, второй подход представляется более рациональным: вместо того, чтобы месяцами разрабатывать систему, внедрять ее и только после этого обнаруживать неудобные для пользователей или ненужные функции, более рациональным видится подход системы Agile. При использовании этого подхода есть возможность оперативно вносить необходимые корректировки, а значит, в результате получить функциональную систему, соответствующую требованиям производства и удобную для пользователей.
Реализация подхода включает в себя прохождение нескольких стадий. Первая и фундаментальная – это трансформация организационной культуры, прежде всего, синхронизация действий вертикальных департаментов через создание единой системы непротиворечивых метрик и внедрения процесса планирования продаж и операций (S&OP).
Единая система метрик позволит компании синергетическими усилиями достигать поставленных целей на всех уровнях: от стратегического до индивидуального – в отличие от подхода, когда KPI для каждого подразделения устанавливаются отдельно, что неизбежно ведет к возникновению конфликта целей. Примером такого конфликта является противоречие между целями трех подразделений производства, продаж и финансов:
Производство стремится производить большие партии с минимумом переналадок оборудования и изменений в плане. Для минимизации рисков срыва сроков желательно иметь большие страховые запасы сырья, готового продукта, а также всех промежуточных полуфабрикатов. Идеалом производства является изготовление монопродукта вообще без каких-либо изменений.
Продажи, напротив, стремятся к расширению ассортиментного ряда и максимальной гибкости (что влечет множество переналадок и короткие производственные партии), также приветствуют страховые запасы, а еще выше ценят возможность работы со склада.
Финансисты стремятся к повышению оборачиваемости запасов и сокращению издержек любыми способами, и прежде всего - минимизацией запасов, а также основных средств.
Единая система метрик объединит усилия всех подразделений компании и направит из на достижение единой цели, например максимизации прибыльности.
Вторая часть трансформации организационной культуры – это внедрение процесса S&OP. Его ключевая особенность – синхронизация действий ключевых подразделений компании: продаж, производства, финансов, маркетинга, HR – через циклический процесс взаимного согласования планов и контроля их выполнения с помощью единой системы метрик. Инструментами ИТ-поддержки этого процесса являются аналитические системы, позволяющие извлекать из хранилищ и анализировать большие объемы исторических данных, эффективно решать задачи прогнозирования с использованием наиболее надежных моделей.
Компании-участники развитых цепей поставок вовлекают в процессы планирования своих партнеров – как клиентов, так и поставщиков, Известны различные подходы, в том числе CPFR (совместное планирование, прогнозирование и пополнение запасов), VMI (склад, управляемый поставщиком), непрерывное пополнение запасов, различные формы консигнационных запасов. Общей чертой этих подходов является тесное взаимодействие между поставщиком и потребителем, включающее непрерывный информационный обмен как в части фактических данных, так и в части планов и прогнозов. Информационная прозрачность всей цепи поставок позволяет свести к минимуму разрушительное влияние «эффекта бычьего кнута», когда случайные незначительные отклонения спроса в конце цепи поставок приводят к сильным изменениям в ее начале.
Синхронизация темпа производства с клиентским спросом, передача этой информации поставщикам предприятия позволят многократно увеличить эффективность взаимодействия: это и снижение затрат на закупку сырья и материалов, и возможность радикально сократить складские запасы, защищающие от волатильных поставок, и улучшение показателей оборачиваемости.
Однако для создания единой информационной системы недостаточно внедрить портал поставщиков или клиентский портал: необходимо продемонстрировать контрагентам их выгоду от участия в обмене информацией. На начальных этапах возможно привлечение с помощью более выгодных контрактных условий.
Оптимизация производственного процесса: прогнозирование и производство под заказ
Ключевой принцип успеха производственного предприятия на рынке – это производить только то, что имеет ценность для клиентов компании и точно будет продано. Следование ему позволяет сократить излишнее производство, минимизировать остатки на складах и заморозку средств компании в непроданной продукции. Чтобы следовать этому принципу, передовые компании развивают свои производственные системы в нескольких направлениях.
Первое направление — это прогнозирование спроса и анализ точности прогноза на постоянной основе. Надежный прогноз спроса дает компании возможность уверенно развиваться в соответствии с принятой стратегией и выстраивать проактивное поведение на рынке. В том числе точно настраивать конфигурацию производственных мощностей, квалификацию и численность персонала, характер и объемы складских запасов.
Однако недостаточно просто рассчитать прогноз один раз в год. Инструмент будет работать только если процесс повторяется периодически, например, ежемесячно, и на каждом новом цикле компания анализирует отклонения и выявляет их причины, корректирует модели прогнозирования и бизнес-процессы, шаг за шагом следуя философии непрерывного совершенствования.
Например, если месяц за месяцем компания прогнозирует меньшие объемы спроса, чем фактически показывает рынок, то, вероятно, отдел продаж занижает план, чтобы точно его выполнить и получить причитающийся бонус. Или, что еще хуже, компания не владеет ситуацией на рынке. В любом случае, систематические отклонения прогноза в одну и ту же сторону говорят о необходимости срочного принятия корректирующих действий. Если же прогноз отклоняется то в «плюс», то в «минус», это говорит о необходимости корректировки модели прогнозирования.
Второе направление – это смещение фокуса в управлении запасами на как можно более раннюю стадию производственного процесса, чтобы повысить ликвидность и оборачиваемость запасов. Действительно, хранить на складе все возможные модификации и вариации готовых изделий чревато тем, что какие-то из них быстро будут распроданы, а какие-то надолго задержатся на складе. Если вместо этого произвести на основании прогноза и хранить на складе только компоненты широкой применимости, а сборку готовой продукции начинать, только имея твердый заказ клиента, то запас становится намного более ликвидным, показатели сервиса улучшаются.
Дальнейшее развитие этого подхода – переход к производству на заказ, когда компания на основании прогноза закупает и хранит на складе только сырье и покупные компоненты, а производство запускает, только получив от клиента твердый заказ. Этот вариант производственной среды хорош тем, что обеспечивает наилучшие показатели оборачиваемости и ликвидности запасов. Но он имеет и недостаток – высокую длительность периода от получения заказа до отгрузки готового продукта, с чем готовы мириться не все клиенты. Уменьшить этот период и тем самым сгладить негативную сторону этого подхода позволяет применение современных информационных технологий обработки клиентского заказа (B2B-порталы), продвинутых инструментов планирования производства (системы класса APS) и автоматических систем контроля хода производственного процесса.
Для некоторых компаний наиболее эффективным может стать применение комбинированных стратегий, например, выполнение финишных операций вне производства – на территории распределительного центра или силами дистрибутора. Таким примером может быть организована фасовка товаров народного потребления в потребительскую упаковку или обрезка кабеля необходимой длины на складе дистрибутора непосредственно перед отгрузкой.
Третье направление – максимизация выпуска продукции без расширения производственных мощностей. Достичь этого можно, применяя различные передовые методы управления производством и опираясь на современные информационные технологии. Приведем несколько примеров из арсенала таких средств.
1. Отказ от ручного управления. Важно понимать, что ручное управление – это неэффективный путь для работы промышленного предприятия, пусть даже в условиях профицита производственной мощности. Ручное управление — это прежде всего зависимость от человеческого фактора, высокая вероятность ошибок и неоптимального распределения ресурсов, медленная реакция на отклонения и изменения. Внедрение средств автоматизации планирования и контроля производства позволяет обойти эти ловушки и сконцентрировать усилия квалифицированного персонала на принятии решений, сняв с них необходимость выполнения монотонной расчетной работы. Кроме того, алгоритмы современных систем планирования имеют инструменты многокритериальной оптимизации производственных расписаний, которые позволяют вывести эффективность использования оборудования на качественно новый уровень. Особенно это актуально для производств, где оборудование не имеет узкой специализации.
2. Применение теории ограничений для поиска узких мест производства и управления производственными мощностями, в том числе концентрация усилий на повышении производительности «узкого места» всеми доступными методами:
организационными (непрерывная круглосуточная работа оборудования без остановки на обеденный перерыв и пересменку),
техническими (внедрение средств ускорения переналадок оборудования),
методологическими (оптимизация производственного плана, создание перед «узким местом» буфера, сглаживающего неравномерную загрузку).
3. Модернизация существующего парка оборудования и методов его обслуживания. Доработка систем управления оборудованием и контроля параметров его работы, включение оборудования в централизованную информационную систему компании позволяет добиться существенного увеличения времени доступности и производительности оборудования. Одним из способов повысить время доступности оборудования является переход на прогрессивные методы ТОиР, в том числе обслуживание по состоянию, когда ремонты оборудования планируются на основании данных, полученных по результатам периодических осмотров или с автоматических датчиков.
4. Применение подходов бережливого производства. Приемы борьбы с потерями разной природы положительно воспринимаются менеджментом компаний и поддерживаются персоналом при выстраивании соответствующей мотивации. Среди таких приемов организация производственных ячеек – небольших зон, в которых сконцентрировано все оборудование, требующееся для производства конкретного продукта, с минимизацией потерь на перемещение и пролеживание изделий между технологическими операциями. В проектах по автоматизации промышленных компаний эти принципы закладываются в ИТ-системы. Более того, опытные консультанты по автоматизации могут внести предложения и по пространственному расположению, и по организации процесса производства.
5. Раннее обнаружение дефектов. Дефект, обнаруженный на ранней стадии производственного процесса, обходится компании намного дешевле, чем его обнаружение ОТК при тестировании готовой продукции. Встраивая контроль качества в производственный процесс с помощью систем автоматического контроля и управления качеством, можно минимизировать риски, снизить себестоимость продукта и улучшить показатели сервиса клиентов.
Таким образом, автоматизация промышленного предприятия – это действенный способ оптимизировать затраты на производство и минимизировать потери,«Кабель. Дополнение к “1С:ERP”» – это ERP-система на базе «1C:ERP» с усовершенствованным функционалом в части планирования (модуль Ortems от Delmia), модулем Odyssey WMS для организации работы складов с учетом отраслевой специфики кабельных заводов. Оно позволяет автоматизировать ключевые бизнес-процессы, повысив эффективность и контролируемость работы кабельного производства.